AutoBauLog - Autonome Steuerung in der Baustellenlogistik
- contact:
- project group:
RIB Informations Technologies AG (Konsortialführung)
Universität Hohenheim, Forschungszentrum Innovation und Dienstleistung (FZID)
Drees & Sommer Infraconsult und Entwicklungsmanagement GmbH
Virtual Dimension Center Fellbach (VDC)
KIT, Institut für Technologie und Management im Baubetrieb (TMB)
- funding:
Bundesministerium für Wirtschaft und Technologie (BMWi)
Förderkennzeichen: 01MA09011
- startdate:
01.10.2009
- enddate:
30.09.2012
AutoBauLog - autonomous control in construction site logistics
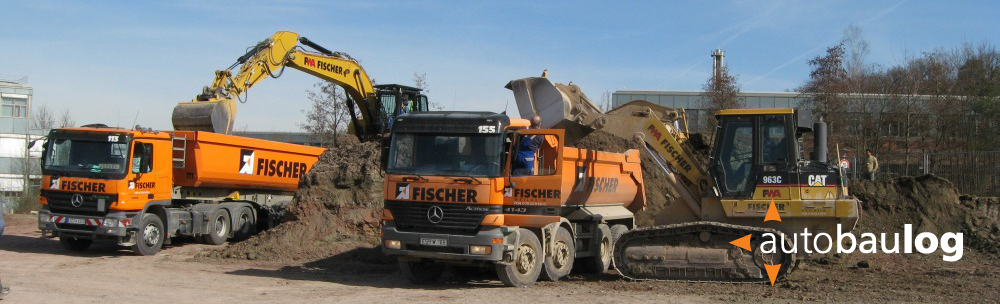
As part of the competition entitled "AUTONOMIK - autonomous and simulation-based systems for medium-sized companies", the Federal Ministry of Economics and Technology (BMWi) is financing the project "AutoBauLog - autonomous control in construction site logistics". The aim of AutoBauLog is to secure a significant improvement in the coordination of the many different actors on construction sites across company boundaries. The solution to securing a significant and sustained increase in the efficiency of large infrastructure projects lies in the transfer of suitable digital-factory IT concepts to management and civil engineering fabrication.
Due to a multitude of changing factors as well as the complex logistical interaction of the participating actors, large infrastructure projects such as road construction projects display a high level of dynamism, meaning that during their execution continuous tuning of the processes is required. However, this is often complicated by multi-level subcontractor relationships, numerous media breaks between planning and execution, and often incomplete information on construction progress and quality, which ultimately results in poor utilization of the available resources. While large-scale use is now made of IT solutions during planning, in the execution phase, despite the permanent information and coordination needs, considerable deficits remain. The solution of the AutoBauLog consortium to securing a significant and sustained increase in the efficiency of large infrastructure projects lies in the transfer of appropriate digital factory IT concepts to the management and civil engineering fabrication. Four performance areas are integral parts of the research project:
- (Sub-)autonomous machine control - fitting of the construction machinery with distributed software-based intelligence, 3D sensor and satellite-based control systems.
- Autonomous machine coordination - enabling construction machinery to coordinate and cooperate internally using software agents, i.e. the possibility to independently form machinery teams.
- Control-room-based monitoring and simulation - the bringing together of machine-based construction processes into a virtual-reality-based control room. Dynamic task distribution on the machine level through derivation from variant simulation.
- Integrated product/building models - the representation and versioning of the actual and target geometries and process information on the control-room level.
The sub-project of the BLM consists in designing for the project context an appropriate integrated product model for civil engineering and the (partially)-autonomized construction site, the "Integriertes Produktmodell Tiefbau (IPT)" (integrated civil engineering product model). Geometric, topological and other semantic information should be determined for the context of the project object, and existing building and city-product model standards (including IFC, CityGML, LandXML) examined for extensibility. When extending the schema, the traceability of semantic status information, references to the process model, the mapping of model-based quantities or areas or volumes, the required geometric representation, as well as the localization of the product model components should all be taken into account. The BLM will develop a "Design/"Autonomik"" partial model based on the acquired findings and requirements.